輕質TPE符合回收材料含量標準
凱柏膠寶輕質系列的擴展標誌著輕質建築領域材料開發的新里程碑。
近年來,各行業對輕質材料的需求迅速增長,這些材料在特定應用環境中具有與傳統材料相當的性能。在這種背景下,輕質熱塑性彈性體(TPEs)作為傳統TPE的替代品,憑藉其回收內容物,發揮關鍵作用。輕質TPEs不僅提供了廣泛的選擇,還具有獨特的材料特性。
Marius Kantoch
Market Manager Consumer | Master Professional (CCI) of Technical Management
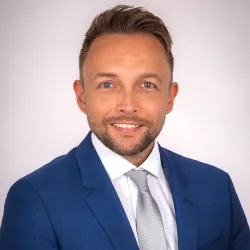
+49 8638 9810-513
再生原材料含量:39%
2010年代末,我司研發了一項技術,能夠生產非常輕質的專用熱塑性彈性體。該技術基於 3M™ 玻璃泡的使用,該玻璃泡的整體材料密度明顯較低,能夠生產具有出色彈性和柔軟度的塑膠相容組件。這些已被證明是成功的新開發的輕質TPE 於2020 年春季推出,其成功的主要原因是因為這些化合物廣泛滿足了汽車製造商以及航空和電動工具等其他行業,或體育和休閒行業的製造商目前對有效輕質化解決方案的需求。
我司輕質TPE系列的擴展標誌著輕質建築領域材料開發的新里程碑。其新開發的凱柏膠寶 R( THERMOLAST® R )化合物具有與現有系列幾乎完全相同的材料特性,並將這些特性與 10% 至 60% 的回收含量相結合。這些來自消費後來源的資源節約型回收原料進一步提升了輕質TPE的優點。這可以減少化合物的產品碳足跡 (PCF),從而對塑膠加工公司許多零件的可持續性和氣候目標產生積極影響。
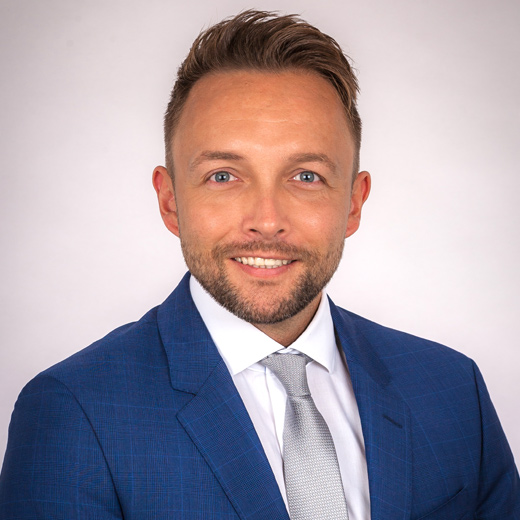
無論我們獲得了哪些優勢,都可以明顯看出,使用回收材料加工輕質TPE因其更短的循環時間而節省了更多資源。
Marius Kantoch | Market Manager Consumer at KRAIBURG TPE
使用具有回收材料含量的輕質 TPE 還可以減輕材料和零件的重量,使得車輛在使用階段的能源會減少消耗。此外,由這些TPE材料製成的組件可以回收並在相同或類似的應用中重複使用。 「無論我們獲得了哪些優勢,都可以明顯看出,使用回收材料加工輕質TPE因其更短的循環時間而節省了更多資源。」消費者市場經理 Marius Kantoch 解釋道。同時,他也補充: 「這再次表明,熱塑性彈性體在可持續性問題上也代表了未來材料的發展方向。」
例如,透過在行動產業或消費產業中使用具有回收材料含量的輕質TPE,與相應的標準TPS 相比,可以減輕約35% 的重量;與TPV 相比,可以減輕30% 的重量;與PVC 相比,甚至可以減輕高達50% 的重量。
我司輕質TPE的其他優點包括在各自的生產過程中易於加工。這意味著它們可用於所有熱塑性塑膠生產線上的注塑和擠出工藝,且零件幾何形狀的收縮率和變形率較低。該材料由於其高表面均勻性和出色的壓縮永久變形性能而取得了良好的效果。此外,具有回收材料含量的輕盈 TPE 還具有柔軟性、阻尼性、表面品質和佩戴舒適性等特點。因此,其可能的應用範圍很廣,其中包括:輕質 TPE在汽車領域可作為電動工具的組件,以及滑雪設備或保護器的大表面和輕質組件等。
我司在全球範圍內都提供具有回收材料含量的輕質 TPE。
關於輕質TPEs
自2020年推出以來,凱柏膠寶的輕質TPE已廣泛應用於許多汽車領域。除了顯著減輕組件重量外,該產品的廣泛應用還歸功於其優越的材料特性,例如減少組件變形、優化循環時間,以及能夠與完全交聯的EPDM材料競爭的卓越彈性。車頂導軌托架、多組分車門密封件、行李箱和引擎蓋緩衝器,以及擠壓密封件等領域的成功應用,證明了這項尚處於初期階段的技術的獨特性能,並激勵凱柏膠寶將永續發展概念擴展到更多方面。
Lightweight TPE meets recycled content
With the expansion of the Lightweight series, KRAIBURG TPE has reached another milestone in material development for lightweight construction.
Industry demand for lightweight materials that have properties comparable to those of conventional materials in their specific application environments has been increasing by leaps and bounds in recent years. The replacement of conventional thermoplastic elastomers (TPEs) by Lightweight TPEs with recycled content plays a central role here. Lightweight TPEs provide wide-ranging options and unique materials parameters.
Waldkraiburg, 15 October 2024 – In the late 2010s, KRAIBURG TPE developed a technology that makes it possible to produce very lightweight application-specific thermoplastic elastomers. This technology was based on the use of 3M™ Glass Bubbles, which, with a markedly low overall material density, enabled the production of plastic-compatible components that are characterized by both outstanding resilience and softness. Launched in spring 2020, these newly developed Lightweight TPEs have proven to be successful. The main reason for this was that these compounds extensively met the current demand for effective lightweight solutions on the part of automotive manufacturers, as well as manufacturers in other sectors such as aviation and power tools, or in the sports and leisure industry.
KRAIBURG TPE’s expansion of the Lightweight series now marks another milestone in the development of materials for the lightweight construction sector. The newly developed THERMOLAST® R compounds have almost exactly the same material properties as the existing series and combine these properties with a recycled content of 10 to 60 percent. These advantages of lightweight TPEs are complemented by resource-conserving recycled raw materials from post-consumer sources. This leads to a reduced product carbon footprint (PCF) for the compounds and can therefore have a positive impact on the sustainability and climate targets of plastics-processing companies for many components.
The use of Lightweight TPEs with recycled content also reduces the weight of both materials and parts. This may lead to a reduction in energy consumption during the utilization phase of vehicles. In addition, components made of these materials can be recycled and reused in the same or similar applications. “Irrespective of any formal advantages that we achieve, it is measurably the case that the processing of Lightweight TPEs with recycled content saves more resources due to shorter cycle times,” explains Marius Kantoch, Market Manager Consumer at KRAIBURG TPE. “This shows once again that, in relation to sustainability issues, thermoplastic elastomers also represent the materials of the future.”
About Lightweight TPEs
Since their launch in 2020, Lightweight TPEs from KRAIBURG TPE have been used in many automotive applications. Along with the benefit of component weight reduction, the product’s key factors particularly include material properties such as reduced distortion of the component, optimized cycle times as well as outstanding resilience that can even compete with fully cross-linked EPDMs. Successful applications in the fields of roof rail carriers, multicomponent door seals, trunk and hood buffers, as well as extruded sealings, confirm the unique properties of this still young technology and are encouraging KRAIBURG TPE to extend the idea of sustainability beyond weight reduction.
The weight reductions achieved by using Lightweight TPEs with recycled content for applications in the mobility sector or the consumer industry, for example, can save about 35 percent as compared to the respective standard TPS, 30 percent as compared to TPV, or even up to fifty percent as compared to PVC.
Other advantages of lightweight elastomers from KRAIBURG TPE include easy processability in the respective production processes. This means they can be used – with low shrinkage and distortion in the part geometry – for injection molding and extrusion processes on all thermoplastic production lines. The material achieves excellent results due to its high surface homogeneity and outstanding compression set. Lightweight TPE with recycled content is also characterized by its softness, damping, surface quality and wearing comfort. So there’s a wide range of possible applications: in the automotive sector, as components for power tools, as well as for large-surface and lightweight components for skiing equipment or protectors, etc.
Lightweight TPEs with recycled content are available worldwide from KRAIBURG TPE.
凱柏膠寶 - 快覽
- 總部與生產基地:瓦爾德克賴堡/德國
- 區域總部和生產基地:吉隆坡/馬來西亞,亞特蘭大/美國
- 產品:熱塑性彈性體化合物
- 品牌:熱塑寶、科柔寶、高溫寶和尼塑寶
- 市場:歐洲、美洲、亞太地區
- 員工:660