Stechampullen und andere Behälter für die Entnahme und Verabreichung flüssiger Arzneimittel erfordern Verschlusskappen mit einer Dichtung, die sich leicht durchstechen lässt und dabei zuverlässig abdichtet. Thermoplastische Elastomere (TPE) setzen sich in diesem Einsatzbereich zunehmend gegen klassische Elastomere durch. Ihr vorteilhaftes Eigenschaftsprofil ermöglicht auch ein Redesign des Verschluss- und Dichtungssystems für erhöhte Funktionalität und wirtschaftlichere Fertigung. Voraussetzung dafür ist eine ganzheitliche Herangehensweise an die Auswahl bestehender Portfolio-Produkten oder Entwicklung und Selektion geeigneter, innovativer TPE-Werkstoffe.
Am Anfang standen Phiolen aus Ton, später Porzellan und Glas. Verschlossen wurden sie meist mit einem Stopfen aus Wachs oder Kork. Seither hat sich viel geändert – und die Anforderungen werden nicht geringer. Denn der Bedarf an spezifischen flüssigen sowie fließfähigen Medikamenten und wässrigen Infusionslösungen steigt unaufhörlich. Darüber hinaus suchen die Hersteller laufend nach neuen Material- und Designlösungen, um ihre Fertigungskosten zu minimieren. Aus den einfachen Fläschchen sind komplexe Behältersysteme geworden. Und in vielen müssen sie auch die Entnahme einer einzelnen Dosis ermöglichen, ohne die Sterilität der verbleibenden Menge zu beeinträchtigen.
Herkömmliche Verschlüsse für Stechampullen, Infusionsflaschen und andere pharmazeutische Wirkstoffbehälter haben heute eine Kappe aus Aluminium mit einer innenliegenden Elastomerdichtung, auch Septum oder Membran genannt. In den vergangen Jahren ist die Skepsis gegenüber diesem System gewachsen. Als Alternative werden immer häufiger Verschlusskappen aus Kunststoff mit einer Dichtung aus thermoplastischem Elastomer eingesetzt. Diese Lösung ist prinzipiell in einem zweiteiligen, verschweißten oder aber in einem Mehrkomponenten-Design möglich, bei dem die TPE-Dichtung im Spritzgießverfahren fest mit dem Kunststoff verbunden wird. Der Hersteller muss dabei die Kompatibilität der beiden Materialkomponenten sicherstellen, um ihre zuverlässige Haftung zueinander und damit die dauerhafte Integrität der Dichtung zu gewährleisten.
Erhöhte Funktionalität
Denn so unscheinbar die Durchstechdichtung auch sein mag, umso anspruchsvoller ist die an sie gestellte Funktionalität. Als Teil des Behältersystems soll sie die abgefüllte Flüssigkeit gegen das Eindringen von Fremdstoffen schützen und beim Lagern und Transport das Auslaufen verhindern. Wenn angestochen, muss sie zuverlässig gegen die Nadel oder den eindringenden Dorn abdichten, und nach dem Abziehen der Nadel ist es notwendig, dass das Material auch die Einstichstelle wieder dicht verschließen kann. Dieses Verhalten wird gern als ‚Selbstheilung‘ bezeichnet, was jedoch in die Irre führt. Die Punktierung bleibt bestehen. Ähnlich wie bei Gummi sorgt die Elastizität des TPE-Materials jedoch für einen Rückstelleffekt, der im Idealfall die verletzte Stelle für die im Behälter verbleibende Flüssigkeit undurchdringlich abdichtet.
Um all dies zu erreichen, genügt es nicht, Gummi in der jeweiligen Dichtungsgeometrie einfach 1:1 durch ein TPE zu substituieren. Zugleich stellt sich die Frage, weshalb nicht gleich das gesamte Behältersystem ‚neu gedacht‘ werden sollte, um die vorteilhaften Anwendungs- und Verarbeitungseigenschaften von TPE voll zu nutzen. Dies betrifft insbesondere die kostengünstigere Fertigung von Verschlusskappen mit fest integrierter TPE-Dichtung in einem Zweikomponentendesign. Wenn die ‚harte‘ Kappe und die flexible‘ Dichtung aus kompatiblen thermoplastischen Materialien bestehen, erhöht dies die Funktionssicherheit der Abdichtung ohne den Einsatz zusätzlicher Haftvermittler. Denkbar wäre auch eine direkte Anbindung an den Behälter, wenn dieser aus Kunststoff besteht, wie etwa bei Infusions- oder Nährstoffbeuteln. Die Zweikomponentenlösung erfordert keine chemische Vernetzung und erübrigt die Kappenmontage, was wiederum den Automatisierungsgrad der Fertigung erhöht und zu einem reineren Endprodukt führt.
Hinzu kommen weitere Funktionen, die sich mit einem ausschließlich thermoplastischen Kappen- und Dichtungsdesign leichter umsetzen lassen, wie Manipulations-, Kinder- und Fälschungssicherheit, letztere beispielsweise durch Integration eines RFID-Chips. Auch eine metall- und glasfreie Ausführung der Endprodukte ist ein gewichtiges Argument.
In Teil 2 erfahren Sie, warum Thermoplastische Elastomere von KRAIBURG TPE sich hervorragend für aktuelle und zukünftige Caps and Closure-Anwendungen im Medizinalmarkt eignen und wie Konformität und Kompatibilität sicher gestellt werden.
Egal ob Sie sich aktuell in der Planungsphase befinden oder bereits Alternativlösungen verwenden – Sprechen Sie uns gerne an. Wir freuen uns auf den Austausch mit Ihnen!
Autor | Oliver Kluge
Market Segment Manager Medical Applications
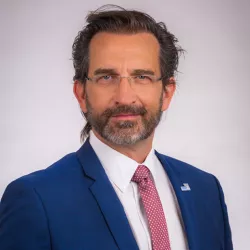
Tel.: +49 8638 9810-479
E-Mail: oliver.kluge@kraiburg-tpe.com
Press | Juliane Schmidhuber
PR & Communications Manager
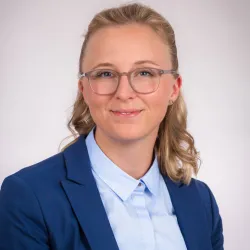
Tel.: +49 8638 9810-568