“Self-healing” protection for liquid medicines – Part 1
Containers for the withdrawal and administration of liquid medicines require caps with a seal that is easily pierced and still re-seals reliably afterwards. Thermoplastic elastomers are being increasingly used for this application.
It all started with vials made of clay, followed by porcelain and glass. They were usually closed with plugs made of wax or cork. Things have changed a lot since then – and the requirements are growing. The demand for specific liquid and fluid medicines and aqueous infusion solutions is constantly increasing. In addition, manufacturers are always looking for new materials and design solutions to minimize their production costs. The simple vials have turned into complex container systems. And in many cases they also have to make it possible to withdraw a single dose, without impairing the sterility of the quantity remaining.
Nowadays, traditional caps for vials, infusion bottles and other pharmaceutical containers used for active agents have aluminum caps with an internal elastomer seal, also called a septum or membrane. In recent years, however, this system has been regarded with increasing skepticism. Plastic caps with a seal made of thermoplastic elastomer (TPE) are being used increasingly often as an alternative. In principle, this solution is either a two-piece, welded design or a multicomponent design, with the TPE seal being firmly combined with the plastic material by injection molding. In this context, the manufacturer has to ensure that the material components are compatible to ensure that they adhere to each other and thus guarantee the permanent integrity of the seal.
Enhanced functionality
Although the pierceable seal looks inconspicuous, the demands made on its functionality are very high. As part of the container system, it is expected to protect the bottled liquid against impurities and prevent it from leaking during storage or transport. When it is pierced, the material must reliably seal against the needle or the intruding spike, and after removal of the needle the material must be able to close the puncture site again in a leak-proof fashion. This behavior is also known as “self-healing” – a misleading term, because the puncture in the material is still there. Ideally, the resilience of the TPE material – similar to that of rubber – closes the puncture site in such a way that the liquid remaining in the container cannot penetrate it.
To achieve all of these features, it’s not enough to simply substitute a TPE with the respective sealing geometry for rubber one-to-one. The question also arises: why not rethink the whole container system to fully utilize the favorable application and processing properties of TPEs? This applies particularly to the lower-cost two-component production process for caps with permanently integrated TPE seals. If the “hard” cap and the “flexible” seal consist of compatible thermoplastic materials, this will increase the functional reliability of the seal without using additional bonding agents. Direct binding to the container would also be possible if it was made of plastics – as is the case with infusion and nutrient bags, for example. The two-component solution does not require any chemical cross-linking and makes mounting of the cap unnecessary. This in turn increases the level of automated production and leads to a purer final product.
Other functions that can be implemented more easily by exclusively using TPEs for caps and seals include child safety and protection against tampering and forgery – the latter by integrating an RFID chip, for example. Another major argument is that the final products are free of metal and glass.
In Part 2, you will learn why thermoplastic elastomers from KRAIBURG TPE are ideally suited for current and future caps and closures applications in the medical market and how conformity and compatibility are ensured.
Whether you are currently in the planning phase or are already using alternative solutions - feel free to contact us. We look forward to exchanging ideas with you!
Autor | Oliver Kluge
Market Segment Manager Medical Applications
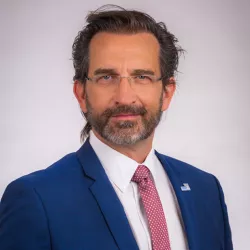
Phone: +49 8638 9810-479
E-Mail: oliver.kluge@kraiburg-tpe.com
Press | Juliane Schmidhuber
PR & Communications Manager
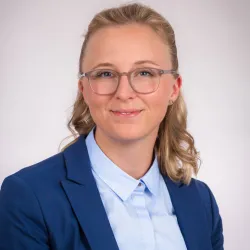
Phone: +49 8638 9810-568