More sustainable TPE for integrated manufacturing of aseptic medical and pharmaceutical packaging
In his blog post, specialist Oliver Kluge talks about TPE that combines excellent processability and high flexibility with reliable steam sterilizability and consumer-friendly haptics.
With the first thermoplastic elastomer on the market specially developed for the blow molding, filling and sealing (BFS) process, a new era in the completely aseptic and highly efficient packaging of ready-to-dose parenteral solutions begins. In his blog post, specialist Oliver Kluge talks about TPE that combines excellent processability and high flexibility with reliable steam sterilizability and consumer-friendly haptics. He also points towards the sustainability aspects of these TPE, which can be of greater interest to manufacturers in the highly regulated fields.
Aseptic means germ-free, and the growing demand for parenteral medical and pharmaceutical products requires largely automated production that reliably eliminates the risk of contamination by germs and foreign particles.
Most glass aseptic packaging forms cannot provide this, as their traditional production, quality assurance and filling involves multiple manual steps. They are also associated with an increased risk of breakage, which is at least incompatible with the trend toward self-administered medications. This has led to the increased use of polyolefins, which are suitable for cost-effective processing in multiple injection molds and automated filling of the containers.
A quantum leap is the completely integrated and aseptic blow molding, filling and sealing technology (BFS), which, however, places special demands on the flexibility and transparency of the materials used. Polyethylenes are predestined in this respect, but reach their limits when it comes to sterilizability under superheated steam at higher temperatures than 110°C. Most polypropylenes can withstand sterilization in an autoclave at 121°C, but they have a high degree of stiffness.
Five integrated steps to an aseptically packaged product
Fig. 1 illustrates the blow molding, filling and sealing process. In the first step, the material is extruded into a tubular film and fed to the blow molding line. There, the tubular film is formed into preforms in a blow mold usually comprising several cavities. The mold closes, squeezes and seals the bottom of the preforms, and mandrels bring them into the desired container shape by means of sterile blowing air. In addition, vacuum can be used. In the third step, the liquid or semi-solid drug is precisely filled in the predefined quantity. The mandrels are then retracted and the containers hermetically sealed with their specific closure system. The mold opens and the finished containers are demolded, removed or ejected.
The entire process is fully automated and aseptic, without intermediate steps or human intervention. The logistics effort is comparatively minimal. Empty containers, their storage, sterilization and feeding are eliminated. Typical applications include ampoules and other small-volume containers up to medium-sized canisters for a variety of medical and pharmaceutical products, such as vaccines and infusions, inhalations and ophthalmics, as well as enteral, wound irrigation, electrolyte and drinking solutions.
Mature TPE technology with distinct BFS advantages
We have developed a THERMOLAST® M (for 'medical grade') grade that overcomes these limitations and also scores with outstanding flexibility and a pleasant feel. The styrene block copolymer-based thermoplastic elastomer (TPS) was extensively tested in the processing pilot plant at BFS market leader Rommelag and successfully sampled for aseptic packaging on fully automated BFS lines. It meets all regulations in this area of application, such as the 2017 VDI guideline for plastics for packaging medical devices and in-vitro diagnostics, and minimizes the forces required for dosing and complete emptying compared to other materials.
Value-creating cooperation from material to customer application
The suitability of this new TPS for aseptic packaging was tested and optimized in close cooperation with our antherindustrial partners. However, the flow index (MFI), which is meaningful for 'hard' plastics, is not a suitable indicator for this. In cooperation with Borealis (Vienna), it was possible to adjust the formulation perfectly for the BFS process.
In addition to in-house extrusion and sterilization trials, processability was then investigated together with Rommelag (Germany) on a bottlepack® BFS line. The tests carried out, followed by successful sterilization trials at 121°C/21min in an autoclave with finished containers, confirmed the practical suitability of the material in the BFS process.
Steps towards more sustainability in highly regulated areas of application
Compounds by KRAIBURG TPE for the BFS process also come with ISCC PLUS certification. By means of mass balancing, compliance with various social and ecological standards benefiting both processors and end consumers is ensured in the course of an extensive review. Also, seamless traceability in the supply chain is taken care of, including proof of origin for feedstock and materials. This certification is especially beneficial for TPE customers in the highly regulated medical sectors, since they do not have to initiate another approval process.
ISCC is a globally applicable, recognized, and standardized certification system that covers bio, bio-circular, and circular raw materials. Gradually increasing the proportion of more sustainable raw materials is possible with the help of the mass balance approach. Fossil raw materials are thus replaced and the CO2e footprint is gradually reduced. This mass balance approach makes it possible to mix renewable and fossil raw materials in production processes. It ensures that the sustainable proportion of the mass balance is traceable. This mass balance approach makes it possible to mix renewable and fossil raw materials in production processes. It ensures that the sustainable proportion of the mass balance is traceable.
Since customers receive a product that is chemically identical to their existing solutions, the current processing parameters, material characteristics and approvals remain unchanged.
Are you interested in more information?
Contact me here or via our website and I’d be happy to talk to you about your applications.
Author | Oliver Kluge
Market Manager Industry
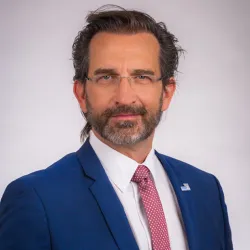
Phone: +49 8638 9810-479
E-Mail: oliver.kluge@kraiburg-tpe.com
Press | Juliane Schmidhuber
PR & Communications Manager
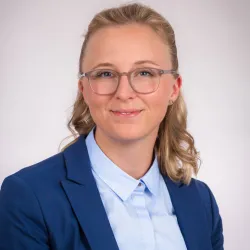
Phone: +49 8638 9810-568