TPE Made from Renewable Resources: Overcoming Challenges and Unlocking Solutions
In her latest blogpost, Magdalena Michl, Product Manager EMEA, focuses on the shift from fossil-based to bio-based thermoplastic elastomers (TPEs).
TPEs made from renewable materials offer significant CO2 reductions, but face challenges when it comes to product implementation. Find out below what kind of obstacles there are when switching to TPE made from renewable materials and how these can be overcome from her perspective.
The shift from fossil-based to renewable and recycled materials is essential to reduce the extraction of finite natural resources and minimize environmental impacts. For manufacturers, bio-based solutions present exciting opportunities, but they also come with unique challenges. In this month's newsletter, we’ll explore the complexities of bio-based thermoplastic elastomer (TPE). Several manufacturers have already launched bio-based TPE, providing significant reductions in the Product Carbon Footprint (PCF). By supporting the transition to renewable raw materials, these TPEs offer both short and long-term reductions in CO2 emissions. However, bio-based materials face hurdles in market adoption. While there is a high interest in recycled content grades, bio-based materials lag in implementation. Why?
From a product manager’s point of view, we have been observing the following three key challenges during last years of developing bio-based TPEs: Technical Performance, origin of raw materials and pricing. But how to overcome these challenges? Well, this requires a combination of collaboration, strategic investments and commitment.
-
Technical performance: Ongoing raw material research and intensive material testing is the basis for demonstrating product performance and providing the market with reliable product solutions.
We have found that there is a wide range of bio-based raw materials that perform comparably to virgin raw materials and today we use many of them in our bio-based TPE portfolio, even for demanding applications with adhesion to polar substrates such as ABS/PC or polyamides. -
Origin of Raw Materials: Feedstock was really just an issue until we decided on our strategic approach and positioning on the use of different generations of feedstock. Our clear recommendation to anyone interested in using bio-based materials is to make up your mind about feedstocks, which ones to use and which ones not to use. It is essential to either have a deep understanding of the raw materials and their background or to work with reliable suppliers who are deeply involved and have a clear positioning.
At KRAIBURG TPE we have decided to focus on the use of 2nd and 3rd generation feedstocks as defined by the EU. 2nd and 3rd generation feedstocks are not suitable for food or feed and include non-food crops, by-products of food and feed production and waste streams. - Pricing: Raw material prices have been a major challenge. We see that price levels are significantly higher than for virgin raw materials, which also reflects the fact that market demand is still at a low level. But it's not an unusual picture when it comes to new raw materials.
A joint approach with suppliers and customers, a clear strategic decision to switch to renewable raw materials and a realistic view of the benefits of bio-based materials are the basis for overcoming this challenge.
Explore our Bio-based TPE
Thermoplastic Elastomers (TPEs) that have a variable proportion of renewable raw materials.
By addressing these challenges, we can unlock the full potential of bio-based TPEs and move the industry towards a more sustainable future. Together we can reduce the impact on the environment.
I'm excited to see where this journey takes us and I'm always happy to talk about different approaches to solutions. Please feel free to contact me at any time if you would like to discuss bio-based TPE.
Author | Magdalena Michl
Product Manager | Product Management EMEA

Press | Juliane Schmidhuber
PR & Communications Manager
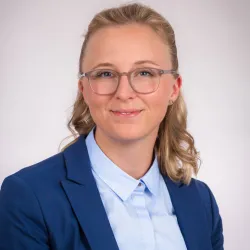